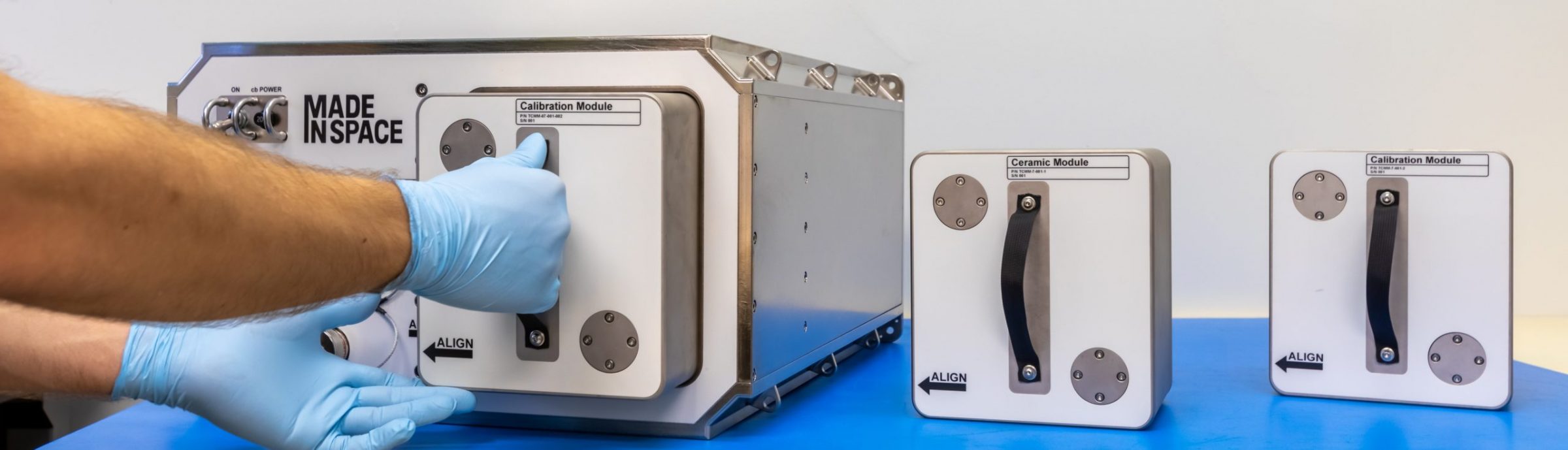
Made In Space (MIS) is set to launch its newest manufacturing facility to the International Space Station (ISS), introducing another brand new manufacturing capability from the MIS team. This significant milestone will be the fifth facility launched by the company and the fifth unique capability brought to the ISS.
The Ceramic Manufacturing Module (CMM) will be on Northrop Grumman’s 14th commercial resupply mission aboard the Cygnus spacecraft. The technology is a commercial in-space manufacturing device designed to provide proof-of-potential for single-piece ceramic turbine blisk (blade + disk) manufacturing in microgravity for terrestrial use. This marks the first ceramic facility on the ISS.
Techniques + Comparison
The Ceramics Manufacturing Module (CMM) is a unique manufacturing technology that introduces both an innovative new manufacturing capability on-orbit and a new material medium to fabricate with. CMM will demonstrate the viability of manufacturing with pre-ceramic resins in an additive stereolithography (SLA) environment. Manufacturing on-orbit in the microgravity environment could enable temperature-resistant, reinforced ceramic parts with better performance including higher strength and lower residual stress, due to a reduction in defects caused by gravity, such as sedimentation and composition gradients that occur in terrestrial manufacturing.
The CMM facility performs a uniform stereolithography printing process that has been validated on NASA-sponsored parabolic flights for high-resolution parts. The initial design process and technical advisory during the parabolic flights were provided by commercial partner, B9Creations. The manufacturing process being flown employs the use of pre-ceramic resins. These resins are the soft materials present before the manufacturing begins that become hardened during the process.

Stereolithography or Digital Light Processing (DLP) is a mature, high-resolution 3D printing approach based on UV curing of liquid resins in a layer-by-layer fashion. Beyond a range of polymers, this method is also used for additive manufacturing of ceramics. To this end, ceramic particles are suspended in the liquid resin. MIS will print an advanced ceramic matrix composite (CMC) material that consists of a pre-ceramic resin reinforced with ceramic particles. The microgravity environment on the ISS is considered especially beneficial for processing such particle suspensions as the settling of particles is mitigated.
This new additive manufacturing process varies in technique from our heritage 3D printing facilities. The MIS Additive Manufacturing Facility (AMF) that has been operating on the ISS since 2016, uses a manufacturing process called Fused Deposition Modeling (FDM). This process builds an object by selectively depositing melted filament material in a predetermined path, layer-by-layer. AMF’s legacy has been the foundation for the technology roadmap and manufacturing programs for MIS while developing new capabilities that will leverage additive manufacturing in space for unprecedented applications.
Industry Applications
The project focuses on advanced materials engineering ultimately leading to reductions in part mass, residual stress, and fatigue. The facility is designed to accommodate additive ceramic sample materials identified by MIS and customers as having the highest value for production. This will help to validate the uniformity, low density, and high performance of printed ceramic blisks as compared with ground analogs. For high-performance applications such as turbines, nuclear plants, or internal combustion engines, strength improvements of even 1-2 percent can yield years-to-decades of superior service life.
Once the manufacturing device returns to Earth, the manufactured blisks are then heat-treated or pyrolyzed to create the final product of a Ceramic Matrix Composite (CMC). CMCs have the potential to perform at hundreds of degrees hotter than the best superalloys and can have a clear advantage over previously used metal components used in aircraft engines.
MIS is developing this technology for commercialization alongside technical partners HRL Laboratories of Malibu, California and Sierra Turbines of San Jose, California.
“Our main interest in utilizing space-enabled materials lies in harnessing the performance benefits they enable for our and our partners’ products, and thus giving us a competitive advantage in meeting demand in these two markets:
1) space vehicle applications, such as satellites in various orbits and spacecraft heading to the lunar and Martian surfaces, that must handle highly reactive atomic oxygen or withstand high-energy particles2) Earth-based high-performance applications, such in Sierra Turbines’ ultra-high temperature turbine blades, where the absence of buoyancy-driven convection and sedimentation allows vastly improved micro-structures not possible to create terrestrially”
Roger Smith, CEO, Sierra Turbines
Single-piece turbine blisks have significant advantages over current assemblies used in aircraft jet engines and integrated rotors. CMCs are typically lighter than high-temperature alloys by 30-50 percent and are capable of handling much higher operating temperatures, measuring above 1100 °C, which can improve fuel economy and efficiency in larger aircraft engines. Successful production in microgravity may provide additional gains in decreasing the mass and residual stress of these parts and increasing their fatigue strength which could convey significant advantages to the aviation industry.


Leveraging Space-Enabled Manufacturing for a Sustainable Low-Earth Orbit Economy
Ceramics produced in microgravity will open opportunities for complex-shaped, temperature resistant, and environment resistant ceramic structures addressing defects common to terrestrial printed parts including porosity and non-uniform shrinkage. The parts that are produced on-orbit will be compared with parts produced terrestrially with MIS hardware as well as commercially available materials.

CMM is part of MIS’s expanding Space-enabled manufacturing portfolio. Space-enabled manufacturing is a form of in-space manufacturing that leverages microgravity to manufacture materials that are either completely new or far superior to their Earth-manufactured counterparts. MIS has a comprehensive suite of ISS rack-based payloads for a variety of advanced manufacturing techniques and facilities with broad applications not limited to proof-of-potential “blisks”. The primary objective for each of these facilities on their first flight will be to demonstrate the technology operates as intended and to produce the material product so that we can analyze those samples on the ground.
These space-enabled materials are realized through the unique microgravity environment that has the ability to alter materials at their atomic level to create a superior product in-space compared to the terrestrial analog of that material. By identifying advanced manufacturing processes that address specific markets and add greater value to the products needed in those markets, along with a scalable approach for meeting the market’s need, space-enabled manufacturing creates a space-Earth value chain to spur commercial activity.
This type of manufacturing represents a key differentiator in how space is utilized for commercial expansion. By leveraging the microgravity environment we are able to economically manufacture new and innovative products that can be sold on Earth. Space-enabled manufacturing is critical to the MIS mission because it creates a profit motive that can scale demand for on-orbit manufacturing capabilities and services which translates to the growth of new markets in the LEO economy and increases demand from terrestrial customers.
Northrop Grumman is targeting liftoff of its Antares launch vehicle for no earlier than 10:26 p.m. EDT Tuesday, Sept. 29, from the Mid-Atlantic Regional Spaceport’s Pad-0A at NASA’s Wallops Flight Facility on Wallops Island, Virginia.