
Research and Manufacturing in Microgravity
With decades of flight heritage developing and operating revolutionary and first-of-kind manufacturing, scientific research, and life sustaining capabilities on board the International Space Station, Redwire has pioneered the technology and expertise required for humans to live and work in space.
Redwire continues to lead the way as humanity welcomes a new era of space exploration. From powering the next generation of commercial space stations, to providing the essential technology needed to enable missions to the Moon, Mars, and beyond, the future of human spaceflight begins with Redwire.
Mission Log
Milestones and highlights from Redwire facilities currently operating on board the ISS.
1st
3D Printer In Space
600+
Scientific Investigations Flown
200+
Objects Manufactured in Space to Date
9
Facilities Currently Operating
7.20.2023

7.18.2023

7.17.2023
This past week, crew aboard the ISS conducted scientific investigations including operations for Plant Habitat-03, which assesses whether epigenetic adaptations in a generation of plants grown in space can transfer to the next generation.

When gravity is removed..
possibilities expand.
Whether you’re developing products to improve life on Earth or planning missions to support the next generation of human spaceflight, leveraging Redwire’s unique space-based manufacturing and research capabilities can help you achieve success.

- Power and Life Support
- Control Panels and Computer Hardware
- Toilets and Sanitation

- Bio-Pharma Formulation
- Disease Diagnostics & Modeling
- Seed Crystals
- Product Consistency

- Tissue Engineering
- Vascularized Tissue
- Regenerative Medicine

- 3D Printed Products & Tools
- Industrial Crystals
- Superalloys and Ceramics
- On-Demand In-Space Production

- In-Space Farming
- Crop Consistency
- Crop Improvment
Heritage & Success
Space Habitation
Pharmaceutical Formulation
Redwire’s cutting-edge hardware operating on board the ISS is proving valuable for pharmaceutical companies that are pursuing new breakthroughs and methodologies, including uniform crystal production and formulation.
Ampli Space Pharmacy Science Kits
Ampli Space Pharmacy science kits, optimized for spaceflight by Redwire.

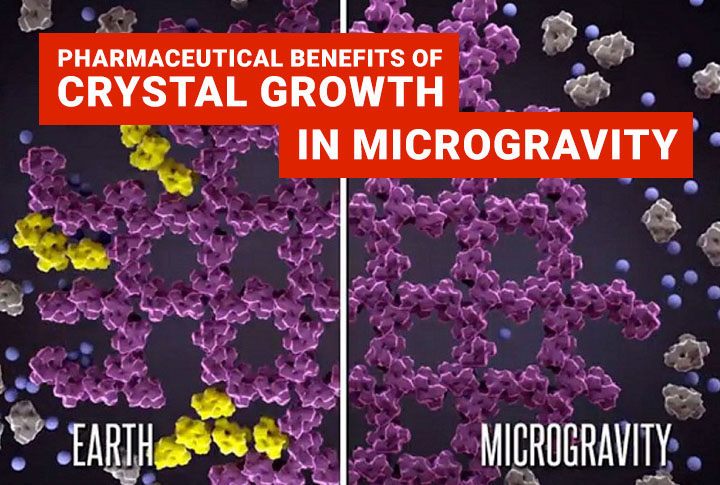
Astronaut Serena Auñón-Chancellor Works With Redwire's Multi-Use Variable Gravity Platform (MVP)
Redwire's Multi-Use Variable Gravity Platform (MVP) is a versatile piece of hardware that acts as a source of "artificial gravity," and provides environmental control and containment. Applications for MVP include cell culturing, tissue chips, organoid studies, drug efficacy and toxicity testing, and even Drosophila studies. MVP not only enables microgravity research, it also allows for comparisons between microgravity, Earth, Moon, and Mars gravity. MVP can aid in the understanding of cancer treatments, treatments of autoimmune disorders, and many other types of diseases.

Redwire's Pharmaceutical In-space Laboratory (PIL)
Redwire's PIL-BOX family of cassettes provides crystallization services for large and small molecule drugs via the batch crystallization method.
- Applications include formulating new crystal morphologies, growing crystals that are difficult to grow terrestrially, growing seed crystals, and growing crystals for structure determination.
- Biopharmaceuticals are often best formulated as microscopic crystals, which have longer ambient stability, lower delivery volume, and novel routes of administration, thus creating longer lasting pharmaceuticals.
- Better biologics and novel methods for biologic delivery benefit both patients and insurers.

Tissue Bioprinting
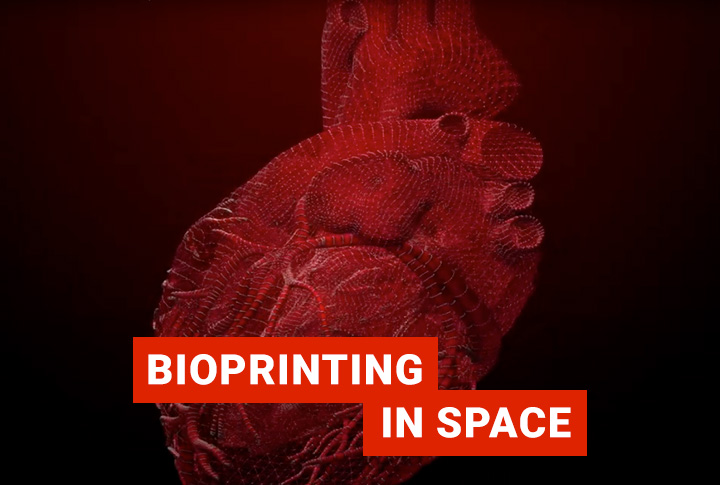
Astronaut Nick Hague Working With BFF Cassette
NASA astronaut Nick Hague conducts science operations inside Europe's Columbus Laboratory module for the BioFabrication Facility experiment. The study is investigating the effectiveness of using 3D biological printers to produce usable human organs in microgravity.

Astronaut Josh Cassada works with Redwire's BioFabrication Facility

Astronaut Christina Koch with BFF Media Bags
NASA astronaut Christina Koch handles media bags that enable the manufacturing of organ-like tissues using the the BioFabrication Facility (BFF), a 3D biological printer. The BFF could become a part of a larger system capable of manufacturing whole, fully functioning human organs from existing patient cells in microgravity.

Manufacturing in Space
A Wrench 3D Printed by Redwire's Additive Manufacturing Facility
Redwire's Additive Manufacturing Facility (AMF) is the first permanent commercial manufacturing platform to operate in low Earth orbit. The versatility and durability of AMF have made it a reliable resource for government and commercial customers since its activation in 2016. It has produced over 200 tools, assets, and parts in orbit.

A Blisk Manufactured by Redwire's Ceramics Manufacturing Module
Redwire’s Ceramics Manufacturing Module uses a technique called additive stereolithography to cure ceramic resin into solid ceramic parts. The process uses a light source to cure resin in very thin layers. Each new layer adheres to the previous one, stacking up to form a complete ceramic part. Ceramics manufacturing offers a unique capability to our in-space partners, allowing themto produce hardware with high thermal resistance. Furthermore, it also offers capability to our commercial partners here on Earth.

3D Print for Radiation Shielding Produced On-Orbit by Redwire's Additive Manufacturing Facility
Radiation exposure is a major hazard for astronauts and could seriously impact their performance and health on or following missions beyond low-Earth orbit. However, any shielding provided comes at the cost of limited and expensive launch mass. Redwire and StemRad are solving this problem by recycling polyethylene from packaging waste into filament for on-orbit additive manufacturing inserts for the AstroRad radiation vests, providing lower launch mass and costs.
As humanity moves beyond low Earth orbit, on-demand local manufacturing technology will become a mainstay for mission planning to address critical needs. Redwire, in partnership with NASA, has demonstrated the efficacy of additive manufacturing to support space exploration and habitation on the International Space Station (ISS) and beyond. AMF is designed as a modular device that is easily upgraded to increase functionality, and is compatible with over 30 polymers, including space-rated, high-performance thermoplastics. This technology enables the rapid iteration and deployment of in-space needs for long-duration missions.

KDP Seed Crystal Produced by Redwire's Industrial Crystal Facility
Redwire’s Industrial Crystallization Facility (ICF) is designed to grow single crystals in microgravity with type and size relevant to terrestrial use. The ICF aims to minimize crystal defects such as inclusions, dislocations, and twinning caused by buoyancy-driven convection, and it grows both large and small crystals of higher quality than terrestrial analogs. Additionally, it facilitates nucleation studies wherein quality, morphology, and size distribution of seed crystals grown in microgravity are studied relative to terrestrial equivalents. Ideal candidate crystals for growth in ICF are industrial optical applications and advanced engineering materials that expand into new product areas not previously investigated.

Turbine Superalloy Casting Module (TSCM) Being Installed on ISS
Redwire's Turbine Superalloy Casting Module is a commercial in-space manufacturing device that thermally processes superalloy parts in microgravity for future use in items like turbine engines on Earth. Superalloys are metal alloys with excellent heat resistant properties. The researchers expect superalloy parts processed in microgravity to have more homogeneous microstructure and improved mechanical properties, such as microhardness.

Crop Production in Space
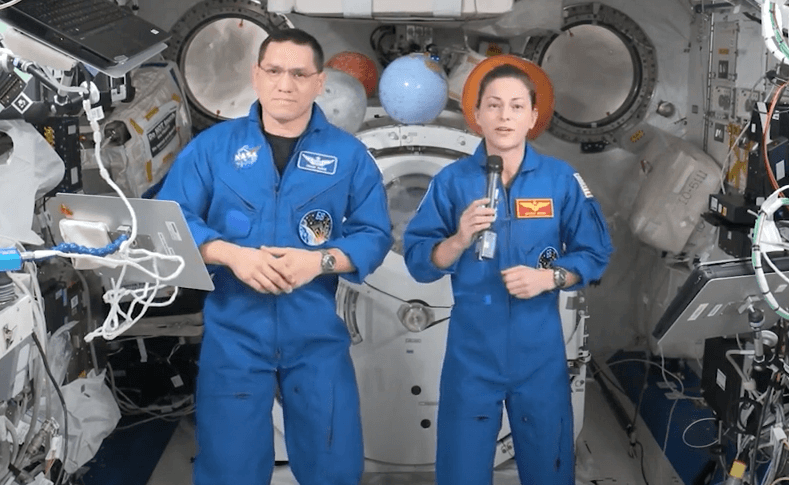
Passive Orbital Nutrient Delivery System (PONDS) Units
The Passive Orbital Nutrient Delivery System (PONDS) device was developed for flight in NASA’s Vegetable Production System (Veggie) facility by Redwire, with collaboration from Tupperware Brands. It can grow a wide variety of plants in space, and requires far less monitoring and maintenance time from flight crews than other plant growth devices.
Up to six of the new units can be installed in Veggie at one time. Like the plant pillows they will replace, the PONDS devices are envisioned to be single use items that will be discarded after the plants are grown and harvested in orbit.

Redwire Greenhouse
Redwire’s Greenhouse provides a privately-owned and operated, commercial platform capable of growing plants from seed to maturity in space. Greenhouse is scalable, to enable research using larger populations of plants or simply taller plants than other on-orbit facilities, and simple enough to be disposable, thereby minimizing cost and precious on-orbit stowage volume. Plants can be rooted in already flight-qualified Passive Orbital Nutrient Delivery System (PONDS) modules, Vegetable Production System (Veggie) Plant Pillows, or other novel support hardware. Greenhouse will enable critical research for crop production in space to benefit future long-duration human spaceflight and expand opportunities for scientific discovery to improve crop production on Earth by assessing how plants respond to the novel environment of microgravity.

Peppers Growing in the Redwire-Managed Advanced Plant Habitat

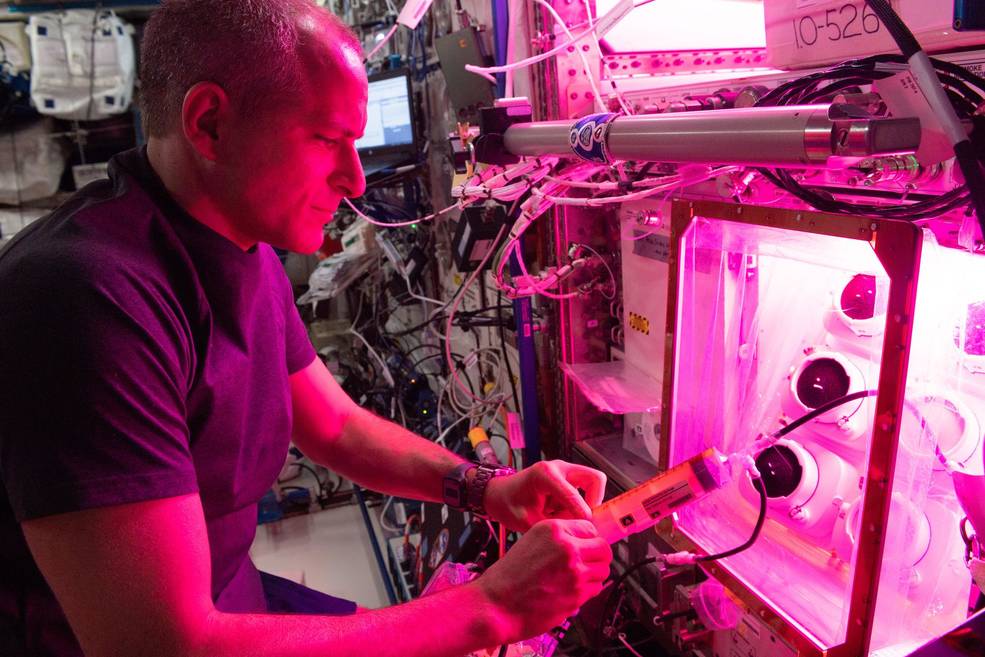